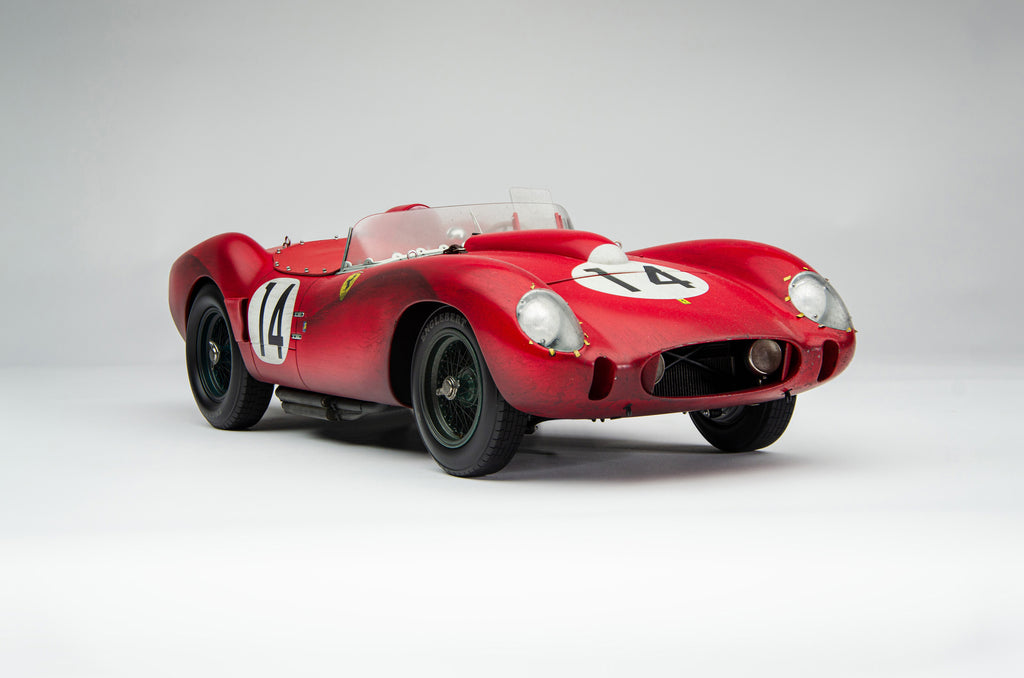
The 1958 Le Mans winning 250 TR of Phil Hill and Olivier Gendebien has been perfectly captured and recreated at 1:8 scale
![]() ![]() ![]() ![]() ![]() ![]() ![]() ![]() |
Bristol, UK, 4th of July 2023
Makers of the world’s finest models Amalgam Collection, today unveiled a new addition to their exclusive collection of Race Weathered models: the Ferrari 250 TR at 1:8 scale. The model is based on chassis 0728TR, as it was raced to a famous victory in the 24 Hours of Le Mans by Phil Hill and Olivier Gendebien on the 22nd of June 1958.
This special series of weathered models is strictly limited to just fourteen pieces worldwide, commemorating the victorious car’s race number. Each model has been meticulously hand-painted and detailed by the artists in the company’s Bristol UK workshop, capturing every detail of the race dirt on the car as it crossed the finish line. Eash model will be accompanied by an archive quality A1 Giclée print of the car driving down the pit lane with the victorious drivers riding aboard, selected by Amalgam from the Motorsport Images collection.
The first model in this edition (pictured) has already been delivered to Wautier Gendebien, nephew of Ferrari racing legend Olivier, who now proudly exhibits a reminder of his uncle’s most significant career moment in his home. Amalgam Director of Brand Sandy Copeman said “It’s always a special feeling to make a personal connection to a racing icon, and it was our privilege to deliver the first weathered to Wautier just recently. The model has perfectly captured a significant moment in his uncle’s racing career, and we hope it will bring great pleasure to Wautier and his family.” Amalgam are now accepting orders for the remaining models in the edition, which will be weathered to order.
Each model is fashioned from thousands of precisely engineered parts and features an opening trunk and a fully removeable engine cover. Underneath the engine cover, accessible only through unfastening the replica leather straps, lies a perfect reproduction of the car’s Gioacchino Columbo-designed three litre V12 engine, complete with an artistically applied spattering of mud and oil. In the trunk, collectors of finely made objects will find the racing fuel tank and the car’s spare wheel, also carefully coated in race grime. Across the exterior of the car, every splash of dirt, mud and oil has been recreated in miniature, including the paint chips on the bodywork and race-worn pieces of tape holding the headlight covers in place.
Amalgam Collection’s Bristol workshop manager Chris Lovatt said “We take great pride in the accuracy of all our models, with exceptional attention applied to the painting of our Race Weathered editions. Our artists have referred to contemporary imagery to ensure each completed 250 TR model is a faithful replica of the real car as it finished the race in 1958. We take pleasure in pushing the boundaries of detail to capture very significant moments of motorsport history.”
The artistic painting of the race weathering is significant, but it is just the final stage in a complex and highly creative process that started with the development of the model. Working with CAD data created from a digital scan of chassis 0734TR, currently in the possession of Ralph Lauren, the artisans developed a prototype, meticulously scaling down the data to ensure that the details are brought to life in miniature. Patterns are created for the individual parts, from which moulds are taken to perfectly cast and reproduce each piece of the intricate puzzle. Development of the 1:8 scale model took over 4000 hours, and only concluded once the experts at Ferrari Classiche were fully satisfied with the accuracy of every aspect of the model. Measuring over 49 centimetres (19 inches) long, each subsequent model takes over 400 hours to cast, fit, fettle, paint and assemble, before the weathering process even begins.
The 250 TR is the sixteenth Race Weathered subject to be developed by the Bristol-based firm at 1:8 scale, and the second 250 TR, after chassis 0732TR, also known as ‘Lucybelle II’, was weathered in 2019 with a limited edition of just three models. The burgeoning collection already includes classic racers such as Sir Stirling Moss’ Mercedes-Benz W196 Monoposto and, most recently, the 1965 Le Mans-winning Ferrari 250 LM raced by Masten Gregory and Jochen Rindt.
The 1958 24 Hours of Le Mans lives long in the memories and hearts of Ferrari afficionados. Gendebien and Hills’ victory there clinched the World Sportscar Championship for Scuderia Ferrari for a third successive year. The race itself was dominated by fifteen hours of rain, three of which were torrential, and saw thirteen separate accidents, one sadly killing gentleman-driver Jean-Marie Brussin. Gendebien and Hill held the lead for 22 hours and, when Hill finally crossed the line, it marked the first ever overall Le Mans wins for American and Belgian drivers, and crowned Scuderia Ferrari as victors at the 24 Hours of Le Mans for the third time. The duo finished a dominating twelve laps ahead of their closest opponents in second place and would go on to be the first pairing to record three victories at Le Mans just four years later. Despite the atrocious weather for most of the race, the winners’ race distance of 4,102 km would still have given them fifth place in the previous year's race. Hill would go on to win the Formula 1 World Drivers’ Championship in 1961, whilst Gendebien remains Ferrari’s most successful racer at Le Mans.
“The Ferrari 250 TR is one of the world’s most sought-after cars, and one of the most successful Ferrari racers that has ever existed” Lovatt adds. “We feel immensely privileged to be collaborating on such a project and are delighted that our model captures every aspect of the original so precisely.”
Amalgam Collections’ Race Weathered Ferrari 250 TR at 1:8 scale is available from www.amaglamcollection.com.
----------------------------------------------------------------
High resolution images can be found here >
EDITORS' NOTES:
MEDIA CONTACTS
PR & Media Enquiries: tom@tomgibsoncommunications.com, T: (201) 476-0322, Mobile: (201) 264-3646
PR & Media Enquiries: pressandmedia@amalgam.com
Director of Brand and Business Development: Sandy Copeman sandy.copeman@amalgam.com
Business and Sales Enquiries: enquiries@amalgam.com
ABOUT AMALGAM COLLECTION AND THEIR HISTORY
- Amalgam are recognised worldwide as makers of the finest hand-made large-scale models. Their work is unique in its attention to detail, with a focus on creating models that truly capture the style and spirit of each car. They have dedicated all their skill and passion to achieving a level of excellence that raises the impact and value of each finished piece to a level far above anything previously created.
- For owners of cars they have already modelled at 1:8 in a limited edition, for which the tooling already exists, they offer a tailormade service, customising a model to perfectly match the specification of the real car.
- For owners of unique very high value cars, Amalgam Collection offer an even bigger 1:5 or 1:4 ‘one-off’ model build from their UK workshops in Bristol, England. They will digitally scan the car wherever it is in the world and take up to a thousand pictures of every detail, allowing them to perfectly and accurately replicate everything at scale. Given the significant number of hours required to develop a unique model the costs are high, so the model is built at a very large scale to maximise the impact and detail, and to deliver the ultimate finished piece.
Amalgam Collection’s design, management and development heart is in England, with extraordinarily skilled and dedicated teams producing the bigger editions in Hungary and China. They are a multinational, multicultural team of crafts-men and women, dedicated to creating the world’s most precise, beautiful and exclusive models. Inspired by the F1 teams and iconic luxury car marques of England and Italy that they serve and partner with, they take huge pride in their mission to perfectly capture the designs, and honour the designers, drivers and creators of the automotive art they love.
Originally a partnership of four talented model-makers formed in 1985, from the start Amalgam created finely tuned models for the most important UK and German designers and architects. Working closely with Norman Foster’s team on the Hong Kong and Shanghai Bank and on the Hong Kong Airport project was a fast, steep learning curve which quickly opened their eyes to subtle aesthetics and refined engineering. Working with such gifted architects their passion and desire to model the very best designs was ignited, which in due course led them to Williams F1 and Adrian Newey who were dominating the F1 championship in 1995, then on to Maranello and to the massively important design heritage of Enzo Ferrari in 1999, and latterly to the works of Pininfarina and Ettore Bugatti.
The seminal performance and luxury car designers of the early to mid-20th century were obsessed with achieving ever higher speeds, lighter and more powerful engines, more streamlined bodies, an impassioned quest that inevitably resulted in elegant and beautiful solutions as a consequence of stretching the supreme excellence of the craftsmanship and engineering to the very limits of what could be achieved at the time.
The companies that today bear these iconic names continue to be inspired, and their creativity is still fuelled, by the extraordinary passion and genius of their founders. Amalgam Collection too find inspiration in the creations of the founders and their companies who continue to design and create automotive artworks.
Recognising the beauty and importance of these designs Amalgam Collection have utterly dedicated their energy and passion to modelling these cars to a level of accuracy, precision and excellence that raises the finished replica to a level far beyond anything previously created. Amalgam have chosen to work at a scale of 1:8 which is widely acknowledged to be the most satisfying scale to comprehend the entirety of a car’s design at a glance, whilst in addition showing the most minute details.
To create perfect scale replicas of modern cars they use original CAD data supplied by the manufacturer and work closely with the design team to perfect their rendition of the interior and exterior finishes.
With regard to classics, in their quest for supreme accuracy and authenticity Amalgam’s team goes to great lengths to locate the best examples of original cars and digitally scans them to capture the precise shape and proportions of every part of the car including the chassis, engine and drive train. In addition, 600 to 800 photographs of every aspect and detail of each car are shot, to ensure a complete understanding of the finishes and detailing. The resulting models beautifully and precisely capture the entirety of the original and are impossible to discern from a real car in photographs.
Amalgam is the only maker of model cars in the world that can be considered alongside a maker of luxury watches like Richard Mille or Hublot. In fact, Richard Mille is an Amalgam patron who recognising a shared passion for engineering detail and perfection has commissioned from Amalgam Collection many unique models of his own cars and those he sponsors.
HOW THE MODELS ARE CREATED
- The patterns are created using original CAD from the manufacturer, or extraordinarily accurate digital scans and hundreds of photographs of an original classic car.
- The patterns are used to create silicon rubber moulds that capture every detail.
- Prototyping resin is used to cast the parts from the silicon moulds. Around 20 to 30 parts can be cast from each mould and then a new one must be made.
- Each model is built from thousands of parts: castings, photo-etchings and CNC machined metal components.
- Genuine car paints and manufacturer or archive colour references are used to spray the bodywork.
- It takes between 2,500 and 4,500 hours to develop the tooling for each model.
- It takes between 250 and 450 hours to cast, fit, fettle, paint and build each model.
Every Amalgam Fine Model Car is made entirely by hand from thousands of parts. Detailed original CAD data is supplied by the car's manufacturer or the race team of the car to be modelled. The process of developing each model and creating the master patterns takes between 2,500 and 4,500 hours of skilled work depending on the complexity of the car, with classic cars taking the longest.
In the case of the classic cars an extremely accurate digital scan is made of the car, and hundreds of photographs of all the details of a carefully selected original car are taken, to ensure complete accuracy and adherence to the authentic finishes and materials. Many parts of the model are machined from metal with the major components hand cast from prototyping resin. Each model is individually assembled by a small team of highly skilled model-makers. In total the time taken to machine, cast, hand fettle, paint, polish and assemble each model is between 250 and 450 hours of highly skilled work depending on the complexity of the car.
The finished model is a very precise scale replica of the original car with every detail perfectly and authentically represented at an 8th of the original size. This is modelling elevated to such a high level that it becomes an art form.
Since 1995 Amalgam have been admired and hugely respected by leading designers and engineers in the European automotive industry, as well as F1 designers, drivers and team principals. Amalgam's models appear on the desks of CEOs and presidents of the world's most important car companies. Due to the extreme accuracy and authenticity of Amalgam's creations, made in small limited editions, they are also much sought after by devoted collectors of fine handmade objects across Europe and in the USA.